How Holcim turns a by-product of pig iron production into a valuable raw material for cement production, and why clean hydraulic oil is indispensable.
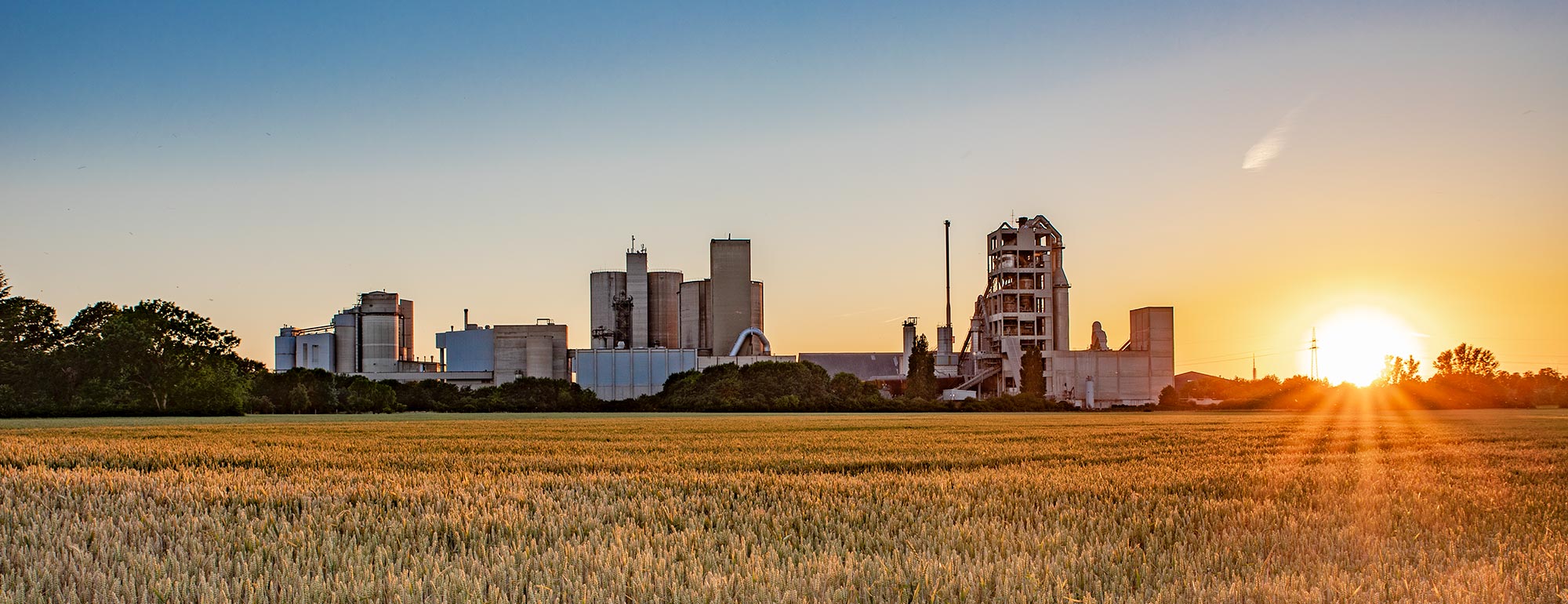
11.03.2024
Clean oil, clean cement production
At its Salzgitter plant, Holcim impressively demonstrates how a by-product of pig iron production is turned into a valuable raw material for making cement. The HANSA‑FLEX Fluid Service provides clean oil in order to ensure that resource-saving recycling works around the clock.
“75% of all hydraulic failures are caused by contaminated oil,” reports Maik Gutjahr as he drives his service vehicle towards Salzgitter. The HANSA‑FLEX Fluid Service technician knows the way to his customer. This is because Holcim has the oil quality of its granulation system checked at regular intervals. “We process up to eight tonnes of pig iron slag per minute from the blast furnace of the neighbouring steelworks. As we work around the clock like the blast furnace, we can’t afford any downtime. The oil analyses give us valuable information about the condition of our plant,” explains Pit Podauke, Production Manager at Holcim’s Salzgitter site.
Sustainable cement production
A channel carries the pig iron slag, which is at least 1,430 °C in temperature, directly from the blast furnace to Holcim’s granulation plant. The water which is added there cools the slag abruptly and granulates it. The result is a grainy mixture of water and slag sand, which is used as a resource-saving raw material in cement production. The high temperatures inevitably produce a lot of water vapour. Holcim collects the condensation water using a sophisticated collection system and then pumps it into cooling towers via a hot water basin. However, the slag sand is still too moist to be used as a raw material for cement. It is therefore transported via conveyor belts to a drainage plant with a total of six silos. Here too, the water is filtered out and fed back into the plant’s operating cycle. Only 0.5 m³ of water needs to be added to produce one tonne of slag sand. The flaps and gate valves for conveying the water and slag sand are operated hydraulically throughout. “With pipelines measuring 600 mm in diameter, this would not be possible otherwise,” comments Pit Podauke.
Clean pipes, clean oil
Maintenance schedules for the plant are closely coordinated with the steelworks. Whenever the operator decides to carry out a general overhaul of a blast furnace, Holcim takes the opportunity to give the granulation plant a thorough inspection. A central component: cleaning the entire hydraulic system. “We always recommend a complete flushing of the entire pipeline system during recommissioning or after an overhaul. This is because contaminants that are already present at the start will continue to be present throughout the entire service life of the system,” explains Uwe Gätgens, Head of the Fluid Service.
Basic cleaning
The centrepiece of the cleaning process is an external flushing unit, which is transported by the Fluid Service on a small trailer. Maik Gutjahr first sets up the flushing circuits and connects the flushing unit to the hydraulic circuit of the system. During an on-site appointment he has previously agreed a suitable setup location and the necessary connections with Production Manager Pit Podauke. The fluid technician draws on his many years of experience when it comes to optimising the individual supply and return flows. This is because a high flow rate of approx. 6 metres per second is required to remove deposits and impurities as effectively as possible. The filter unit used by HANSA‑FLEX removes particles down to a size of 3 µm. For purposes of comparison: a human hair is 40 to 120 µm thick. The same oil used by Holcim is used for the flushing process. It is initially heated to approx. 50 °C. “On the one hand, because warm oil has lower viscosity and therefore flows better. At the same time this expands the pipelines slightly, which makes it easier to dislodge deposits,” says Maik Gutjahr, giving an insight into the practical process. If the oil temperature becomes too high, the oil flushing unit automatically cools it down again.
The external flushing unit (red) can be seen here in the centre-left of the picture in the background. Source: Photographer Timo Lutz
Cleaning the oil tank before Maik Gutjahr fills the system with new hydraulic oil is also part of the routine. For this purpose the fluid technician uses a special suction unit to remove any oil sludge from the bottom of the tank. Specially developed lint-free oil cloths are used to clean the inside walls. Filling the tank with fresh oil – as well as emptying it – is carried out by a bypass filter system. A test run of the hydraulic power pack and acceptance by the customer form the regular conclusion of the job.
Complete documentation
Measuring the purity class in accordance with DIN ISO 4406 is also one of the tasks of the Fluid Service. For this purpose Maik Gutjahr installs a particle counter on the return line of the hydraulic circuit. The number of particles as well as the temperature and relative humidity in the oil are automatically determined, analysed and transferred to a laptop. This provides immediate documentation of the application as required by the standard. “We can discuss the verification of the achieved cleanliness class directly on site with the Fluid Service technicians,” adds Pit Podauke.
HANSA‑FLEX is a true system partner for us, covering the entire spectrum of hydraulics.
Pit Podauke
Production Manager at Holcim
Tight time schedule
In addition to the Fluid Service, other HANSA‑FLEX departments are also involved in the overhaul of the plant. For example, Holcim also takes the opportunity to have hydraulic cylinders overhauled by HANSA‑FLEX and to replace hose lines and pipelines where necessary. “HANSA‑FLEX is a real system partner for us, covering the entire spectrum of hydraulics,” says Pit Podauke, summarising the long-standing collaboration. The Production Manager particularly appreciates the fact that he can always rely on a wide range of operations being completed within the specified time schedule.
Learn more
- 02.03.2024
Your system partner for hydraulics
HANSA-FLEX – Ihr Experte für Hydraulik und Fluidtechnik. Entdecken Sie maßgeschneiderte Lösungen für Ihre individuellen Anforderungen.Find out more