The horizontal drilling rigs from AT-Boretec work with hydraulics
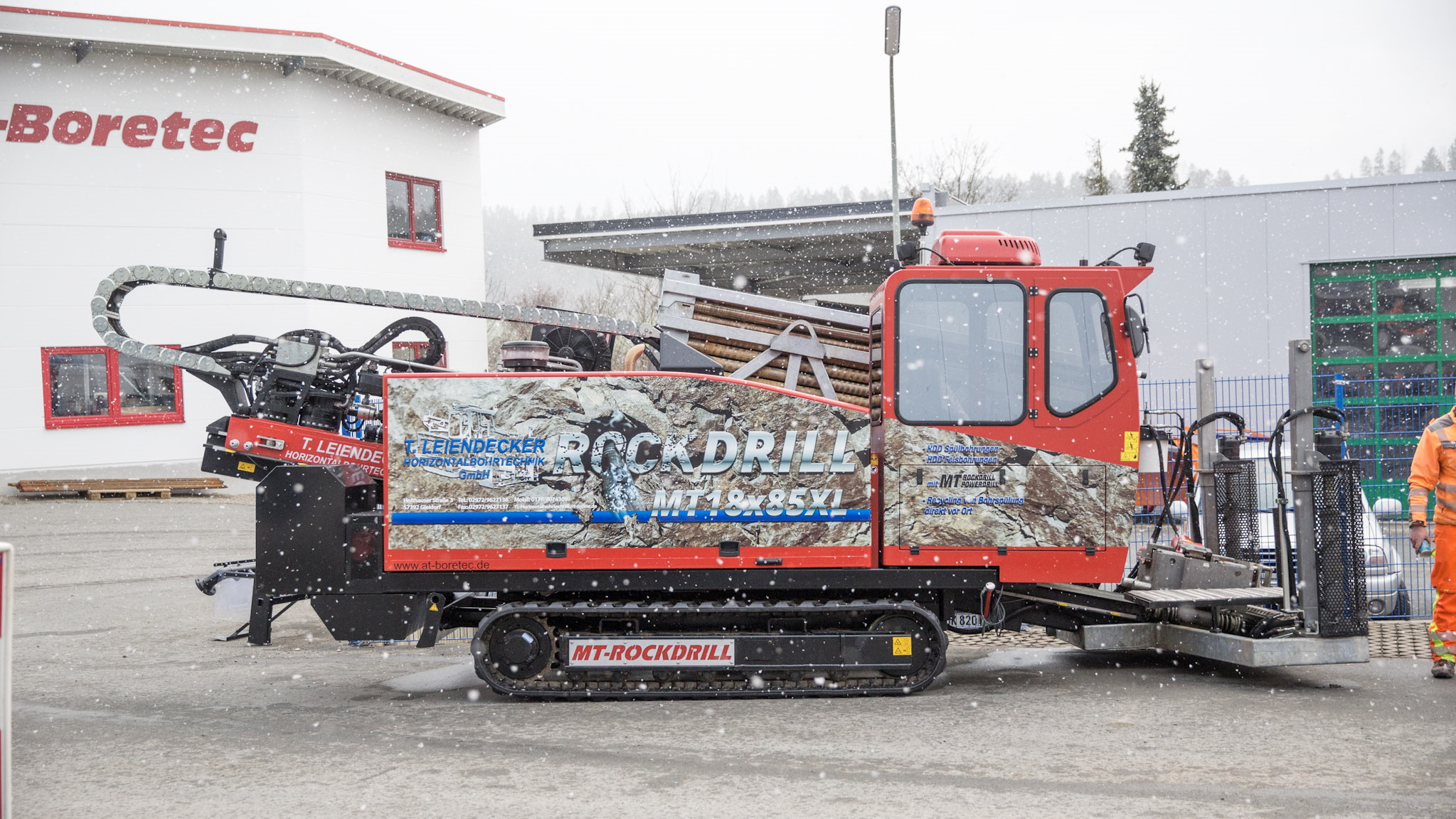
12.03.2024
Drilling instead of digging
If cables need to be laid under roads, rivers and railway tracks in a quick, cost-effective and environmentally-friendly manner, horizontal drilling rigs come into their own. These use directional drilling and make it possible to lay gas and water pipes, power and telecommunication cables and district heating pipes underground without the need for an excavator to additionally dig out a trench. The power for creating the bore holes, which can stretch up to several hundred metres through soil, sand and rock, is provided by hydraulics. The components are provided by HANSA‑FLEX.
With a maximum torque of 15,400 Nm and traction of 350 kN (35 tonnes), the performance data of the MT35 Powerdrill drilling rig from the drilling technology specialist AT-Boretec is impressive. “The efficiency of the horizontal drilling rig is provided by four independent and highly efficient hydraulic circuits”, explains Andreas Willmes, an operations manager at AT-Boretec. The energy for the central hydraulic system and its pumps is supplied by a powerful Deutz diesel engine with almost 250 HP. It is not only the chain drive of the self-propelling drilling rig that is hydraulically driven but also the drill pipe with drill head. The tensile and rotary forces thus provided for the drilling process enable powerful propulsion into the earth. The rotation and propulsion are controlled using two joysticks in the driver’s cab. “Experience is essential when operating the rig”, comments Mr Willmes.
The drill pipe is made up of 4.5 metre long rods that are stored on the drill rig. Once the first rod is in the ground, the drill carriage retracts and a new rod is loaded. The drill rig can carry up to 60 drill rods (270 metres) on board. The hydraulic rack and pinion drive provides sensitive advance and retraction of the drill pipe. The drive itself has a drag chain to protect the hydraulic lines. Once the drill head has reached its target, the retraction pulls lines and empty pipes into the drilled channel. During drilling, a bentonite flush is pumped through the drill pipe to the drill head. The mud exiting the drill head carries the dissolved solids out of the borehole and serves to stabilise the bore channel. The horizontal drilling rigs from AT-Boretec thus achieve distances of up to several hundred metres per day, depending on the soil.
Do it yourself
At AT-Boretec, the drilling rigs are all based on the same design principle but their different sizes and customer-specific versions made it far more difficult to stock ever varying parts like hose lines. The resultant material shortages gave rise to time-consuming procurement trips, often on evenings or at weekends. During discussions with the HANSA‑FLEX branch in Arnsberg-Hüsten, a simple yet impressive idea was born: why not press the hydraulic and water hoses themselves? Once the basic requirements had been established, HANSA‑FLEX delivered a complete workshop set-up with a press, cutting tools, peeling machine, roller, embossing machine and testing tools.
Successful knowledge transfer
The staff at AT-Boretec then acquired the necessary expertise through training courses at the HANSA‑FLEX branch. These not only covered the cutting, assembly and pressing of hose lines, but also the selection of materials and components on the basis of data sheets and the subsequent quality assurance processes. One employee already had experience in the hydraulics sector, which made introducing the in-house hose production process easier. “We are now able to press our own hydraulic hoses. This new independence greatly simplifies production”, comments Andreas Willmes. The required standard of quality was proven through random sampling, during which the hose inspections on the HANSA‑FLEX branch’s test bench were passed without issue.
Everything in stock
Hoses, fittings, seals, attachment materials and other frequently required components are available to AT-Boretec in a consignment warehouse in the production area itself. The warehouse layout is regularly adapted and expanded. “During the weekly visits by the HANSA‑FLEX sales representative, we not only discuss the quantities required but also obtain valuable advice about material selection. In this regard, it is not only the high stresses and strains during operations that play a role but also legal requirements, such as those established by the Machinery Directive”, reports Andreas Willmes from experience.
Smaller repairs such as the replacement of a damaged hose line are usually carried out by AT-Boretec’s customers themselves, not least for reasons of time.
Short channels
AT-Boretec customers generally conduct their own minor repairs, such as the replacement of damaged hose lines, for time reasons. “The tight-knit network of HANSA‑FLEX branches is a real bonus for our customers. Spare parts are available in all areas at short notice – both nationally and internationally”, explains Andreas Willmes. If more complex repair or maintenance activities are required, the drilling technology specialist uses its close cooperation with the mobile hydraulic service. Hose lines are directly pressed at the drilling rig’s site and immediately installed.
“HANSA‑FLEX’s dense network of branches is a real plus for our customers here. Spare parts are available everywhere at short notice – both nationally and internationally.”
Andreas Willmes
Division Manager AT-Boretec
Trusted system partner
AT-Boretec consistently uses a small supplier base. “This affords us not only benefits in relation to purchasing, but also better support”, comments Andreas Willmes. HANSA‑FLEX has now become a firm system partner in the field of hydraulics and water. In addition to the broad product range, AT-Boretec particularly values the exceptional ability to deliver: “Speed is the be all and end all for us. As we often require parts at last minute, the overnight delivery of all types of components is essential for us”.
Learn more
- 12.03.2024
Gearing up for an underground attack
The Gotthard Tunnel: the building project of the centuryFind out more - 10.03.2024
60 years of HANSA-FLEX
Bremen businessman Joachim Armerding founded the HANSA‑FLEX company 60 years ago in the garage of his house near Bremen. His business concept was timely, his motto as simple as it was ingenious: Fulfil the wishes of your customers more rapidly, more flexibly and more fully than all your competitors and never forget the human side and enjoyment…Find out more