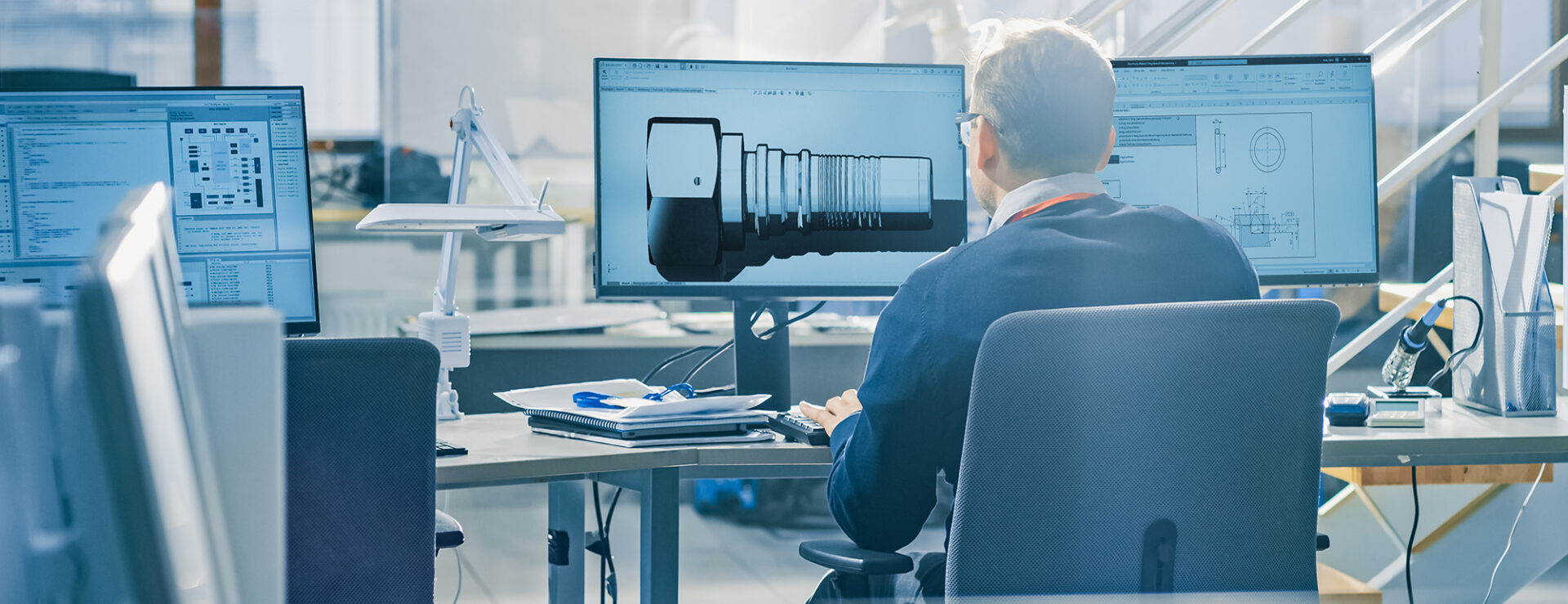
COMPONENTS ENGINEERED BY HANSA‑FLEX
HANSA‑FLEX develops high-quality components in-house to its own quality requirements. In this way, we can reliably provide high product quality independently of suppliers. We call this “engineered by HANSA‑FLEX”. Our technical specifications are consistent and the quality of our products exceeds that required by the legally applicable standards. Our highly qualified engineers produce products to the customer’s specific requirements in our own manufacturing facilities.
IN-HOUSE ENGINEERING FROM ANALYSIS TO SERIES PRODUCTION
The comprehensive know-how of our employees and the use of state-of-the-art equipment form the basis for the design of high-quality components engineered by HANSA‑FLEX.
Our development team provides all the services you require
HANSA‑FLEX coordinates a complex development process at the end of which you receive the product of proven quality. This process involves five steps:
- Analysis and advice
- Drawing and simulation
- Tests on the prototype
- Checks of initial sampling
THE COMPONENTS DEVELOPED BY HANSA‑FLEX COME WITH THESE ADVANTAGES
In-house developments from HANSA‑FLEX provide numerous benefits to our customers. Our own design and manufacturing capabilities mean we are independent of suppliers and are able to ensure high product quality and fulfil delivery promises.
Cohesive system
HANSA‑FLEX components are perfectly matched to one another for optimum performance.
Consistent dimensions
The series produced articles have a consistent appearance and dimensions, which means the installed system is as good as the designer intended
Sustainable quality
Our in-house manufacturing requirements and tests ensure a sustainable high level of quality.
Standards and approvals
We observe about 1,500 standards and have special industry approvals.
YOU CAN DEPEND ON PRODUCTS DEVELOPED BY HANSA‑FLEX
Contact us today
LEARN MORE ABOUT THE DEVELOPMENT PROCESS AT HANSA‑FLEX
- Advice
- Simulation
- Inspection
- Quality assurance
- Item 1
Analysis and advice
Orders for our development services come about in various ways. HANSA‑FLEX employees identify a need in the course of their normal work, strategic considerations suggest expanding our portfolio or customers place a specific development order. In every case, the first step is an analysis of the customer’s requirements. What should the new development achieve? What is its purpose? Then our team discusses preliminary approaches we could take to arrive at the best solution in terms of technical and cost-effectiveness.
- Item 1
From the drawing to the simulation
From these preliminary considerations, HANSA‑FLEX comes up with specific proposals for action and eventual implementation. Engineers then create sophisticated 3D models on the computer. Still in the virtual world, initial trials help to ensure that the process is designed to be as efficient as possible. Using state-of-the-art finite element methods (FEM), our engineers check whether the component on the drawing achieves the required physical properties. The software calculates how the component performs under specific loading such as compression, tension or temperature fluctuations.
- Item 1
Extensive tests on the prototype
Following success in the virtual trials, the component has to produce its predicted performance in practice. This requires us to manufacture several prototypes. Tests in our in-house laboratory confirm whether the properties fundamental to the required hydraulic performance have been achieved. On burst pressure test benches, we check whether the component withstands the required pressure loadings including safety reserve. In the impulse pressure test, we ensure that the component can withstand an adequate number of alternating load cycles and pressure peaks.
- Item 1
Initial sampling
Once the prototypes have proved that the performance of the component meets the requirements, it is released for series production. However, the quality requirements at HANSA‑FLEX are so high that this is not the end of testing for a new product. The first products from the preliminary series are subject to more tests in the laboratory. In our practice-proven Production Part Approval Process, we carefully check whether important features such as dimensions and material choice comply with the specification. Only after this final stage does the new article receive approval for delivery to our customers.
SOPHISTICATED QUALITY ASSURANCE
HANSA‑FLEX subjects its products to a comprehensive quality assurance process. To do this we use high-precision equipment.
The inspection tools we use include coating thickness meters, which, for example, check the correct application of a coating or paint. We use high-tech 3D laser scanners to check dimensions. Our automatic laser scanners compare the component with the relevant drawing automatically so that checks can be made quickly, reliably and precisely, even with large production volumes.
THESE TOPICS MAY ALSO BE OF INTEREST TO YOU
Hydraulic hoses
Hydraulic hoses transfer fluid safely through the system. Their flexibility means they need very little installation space. The HANSA‑FLEX range includes elastomeric…
Find out morePipe fittings
Transitions between components in hydraulic systems are always a point for careful consideration. Pipe fittings from HANSA‑FLEX are standardised in accordance with…
Find out moreSealing technology
Hydraulic and pneumatic systems are only as good as their seals. Just one defective seal can lead to long downtimes…
Find out more