With more than 26 years of experience in the development of wind turbines, Nordex SE is one of the major players in its field.
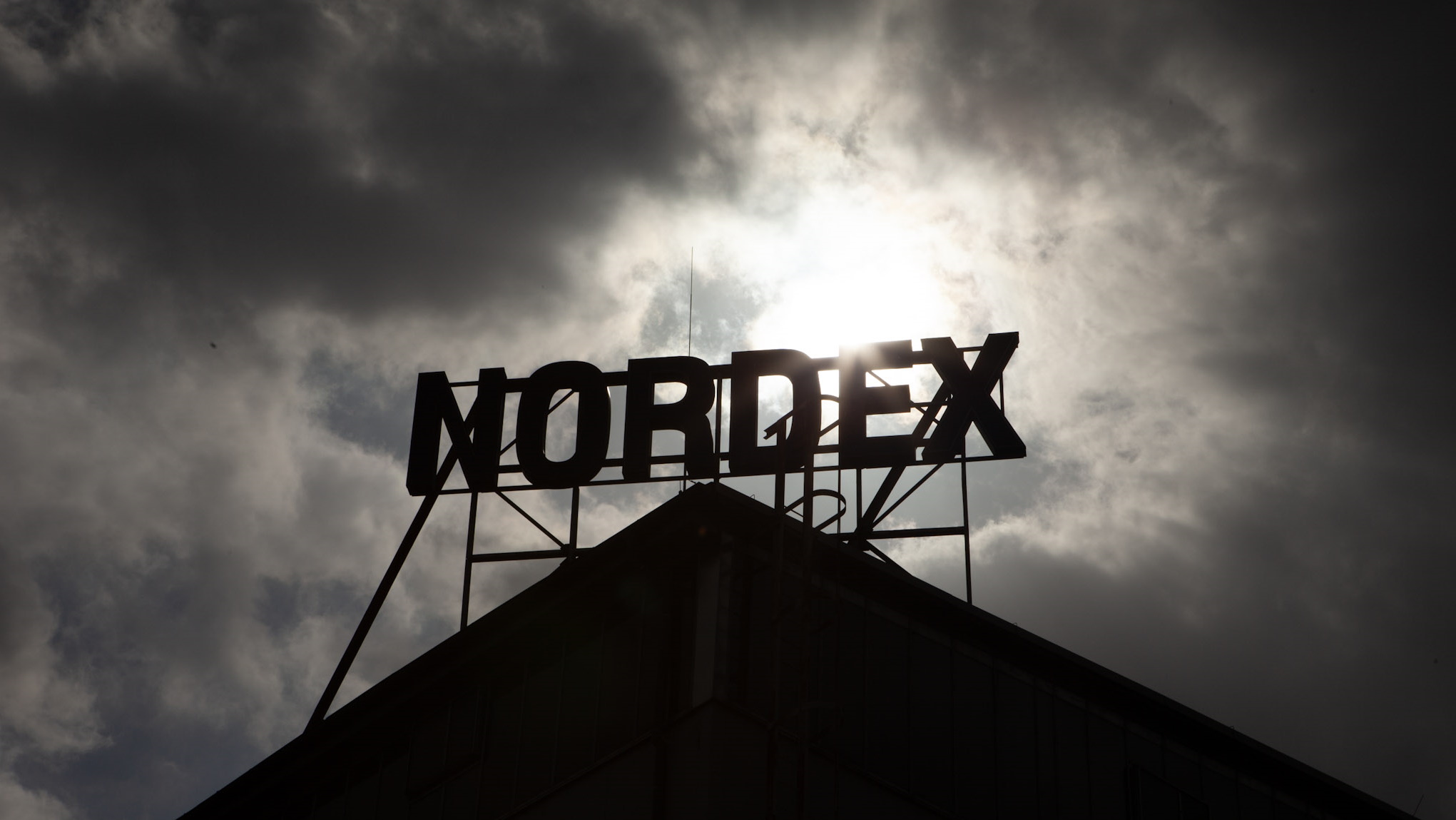
12.03.2024
Harvesting the wind
In the last few years, the use of wind energy has seen advances unparalleled in practically any other technology. With the introduction of new production processes and materials, wind turbines can now be put to profitable use even in regions where winds are relatively calm. With more than 26 years of experience in developing ever larger, and thus more economical systems, Nordex SE is one of the pioneers of this process.
Since it was founded, Nordex SE has installed more than 5,000 wind energy plants, with a combined rated output of 7,000 MW. This is the equivalent of about seven atomic power stations. With its product family, the wind turbine manufacture offers trend-setting solutions for all geographic regions. So they are equally at home with designs for inland or coastal installations, in high or low wind regions. With many years of wind energy expertise, systems engineering and customer-oriented product developments, Nordex has the right system for each of these regions in its portfolio. And the remarkable thing is: Even in places where extreme conditions prevail, such as deserts or the permafrost belt, the systems from Nordex turn ceaselessly in the wind and deliver clean electricity.
Constant refinements
At the same time, Nordex is still a driver of innovations in the industry. Today, most of the company’s experience relates to the market segment for 90-metre rotors. For machinery components, their modifications and the new solution approaches to be implemented in the systems, Nordex conducts an FMEA (Failure Modes & Effects Analysis). One component after another is subjected to “What if…?” scenarios and its behaviour in emergency situations is examined. For example, what if the power fails in the unit? The possible failures and their effects are examined and evaluated. In this way, the quality, safety and reliability of the structures are being improved all the time. New solutions are not incorporated into volume production until they have passed a whole range of such tests.
Brought into line
But Nordex is breaking new ground not only in the development, but also the production of wind turbines. Accordingly, the main European production facility in Rostock has undergone a major modernisation according to industrial principles, which has raised efficiency and production quality at the plant substantially. “We are focusing more intensively on professional volume production to increase our competitiveness”, Dr Marc Sielemann, management board member with responsibility for production, explains the modernisation initiative. This becomes clear when one visits the production halls in Rostock. There are a lot of similarities with automobile construction. In all, three production lines have been set up for the main components, the nacelle, the hub and the generator. Three more lines are dedicated to preassembly. Each station on a production line is associated with a number of clearly defined work steps. With these standardised processes, high product quality is assured. At the same time throughput times were cut and capacity has been tripled with a two-shift system. Today in Rostock, they can produce 1,000 units a year. This corresponds to an output of 2,500 MW.
Entering the offshore market
At the Hanover trade fair this year, Nordex showed once again how much original thinking is being done at the company. SE unveiled its plans for entering the offshore market segment, which the company has not supplied in the past. Experts believe that with an annual sales volume of more than five gigawatt, the offshore market will enter a first maturity phase starting in 2015. Nordex has been preparing for this for the last two years. “The linchpin of our strategy is the development of a competitive product. And in doing this we are following the trend towards the “third generation systems”, which are characterised by significantly higher nominal output combined with lower specific weights. This will be the only way to develop a market of viable volume in the medium term”, explains Thomas Richterich, managing director of Nordex SE. And it is clear: Nothing is being left to chance. This applies to service as well.
Comprehensive service
Twenty-four hours a day, seven days a week, Nordex monitors the availability of every single one of its wind turbines. Service personnel in the regional support centres provide rapid, prompt service on site. HANSA‑FLEX is an important supplier for the service department as well as for production. For modernising existing towers, HANSA‑FLEX delivers complete upgrade kits, for example valves with higher ratings for upgrading the brake systems. And this is where the tightly interconnected branch network pays dividends, because wherever a wind turbine is standing, the nearest HANSA‑FLEX branch is not far away. At the same time, Nordex employees are not just concerned with the flawless operation of their wind turbines, the company has also dedicated itself to conservation of the environment. The protection of bats, for example. Since these are protected animals, it is difficult to erect wind parks in the bats’ territory. So Nordex joined forces with a partner to develop an astonishing solution. Depending on their species, bats fly more frequently at certain times of the year, and of the day, and also in certain weather, temperature and wind conditions. This data has been stored centrally as a number of algorithms which are constantly being compared with the current conditions at the site. As soon as the computer predicts a high probability that bats will be flying, the wind turbine is switched off automatically. This has led to a demonstrable reduction of 70 to 80 percent in bat deaths. At the same time production fell by just 0.2 percent.
Just in Time
HANSA‑FLEX passed a comprehensive series of audits to qualify as a supplier for Nordex several years ago. Since quality will always carry the day, the branch in Bentwisch delivers many of the hydraulic components and hoses, threaded fittings and clamps that are installed in the structures on a “just-in-time” basis. This means, they arrive precisely at the time they are needed. With bent pipes coming from the pipebending centre in Schönebeck and special fittings from Dresden, Nordex uses a wide range of HANSA‑FLEX products in its production processes. And in planning as well, Nordex relies on the hydraulics expertise of our technical consultants. So the services of our hydraulic specialists were enlisted in order to optimise and reduce the costs of new systems. Further development in the field of wind energy will certainly not stand still. And Nordex will just as certainly remain a driving force for innovation in the industry. And HANSA‑FLEX will gladly continue to lend assistance as a reliable supplier.
Learn more
- 12.03.2024
Obtaining energy from waste
In the Stapelfeld waste-to-energy plant, waste is used to generate electricity and heatFind out more